
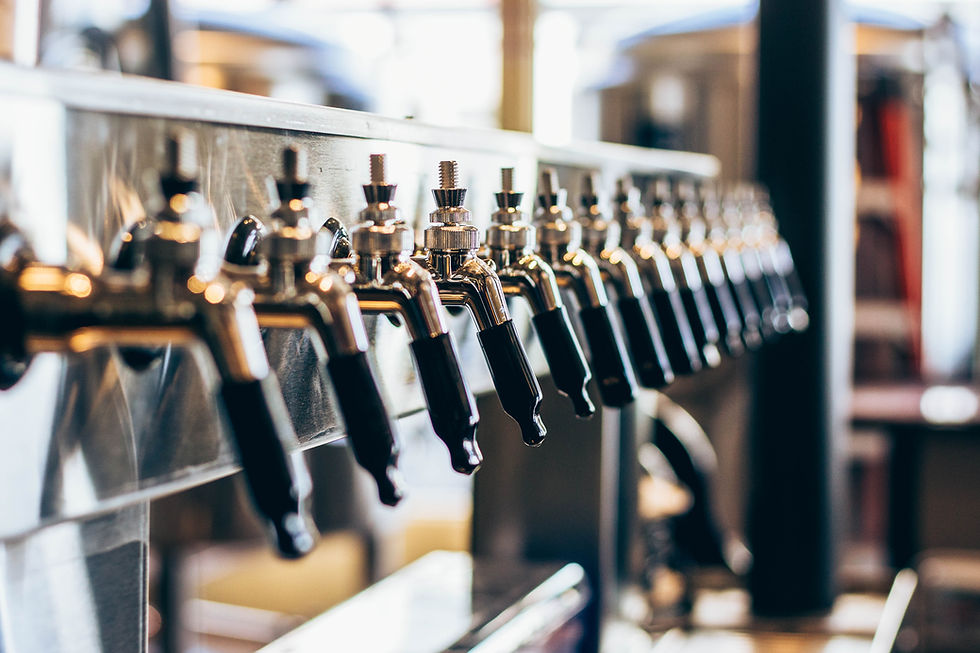
Sustainability within
Drinks Systems
CLIMATE CHANGE
The advance of climate change and the government’s commitment to a net zero carbon target by 2050 has paved the way for all industries to implement sustainability and carbon-saving policies. The hospitality sector is no exception. However, there are still many critical areas where hospitality is missing opportunities to save costs and carbon emissions.
In 2021, the Hospitality sector contributed over 6% to the UK’s GDP and represented over 7% of total UK employment. Pre-pandemic, its contribution to GDP was closer to 10.5%. Consequently, the sector has a proportional responsibility to participate in the drive toward carbon neutral.
​
SUSTAINABLE PRACTICES
A number of drinks providers and manufacturers have committed to carbon neutral practices and are employing various methods to deliver on those promises. Arguably, the most prominent of these is Brewdog which has already received Positive Planet Certification for being a carbon negative company.
In addition, they’ve bought a large plot of Scottish Highlands to create a woodland, and are working with vendors to achieve carbon reduction targets. They’ve also commited to having an electric-only fleet of delivery lorries and are working with suppliers to encourage the use Brewdog-generated bio fuels. All highly commendable initiatives. Changes in production to embrace more sustainable methods is just one area of this industry that needs addressing. A key overlooked area is the drinks systems, and specifically, the cooling of the final product.
​
SOLUTION
A sensible, cost-effective and sustainable solution for the Hospitality sector would be to use heat recovery systems that use rather than waste the heat generated by cooling systems.
Such recovery systems are available: they represent an increased cost on CapEx but result in a decrease on operational cost.
Consider this: the bulk of heat generated from the cooling system within a venue is during its busiest time when there is peak demand on hot water. Even if the latent heat is used only to heat the hot water in the toilets, it would represent a saving on both energy consumption and operator costs. Furthermore, the marketing value of such an operation would be considerable particularly at a time when consumers are becoming increasingly focused on supporting enterprises exhibiting environmentally-conscious credentials.
​
SYSTEMS
As chillers cool the drinks, they displace heat into the environment. The cellar cooling system then has to work harder to compensate for the additional heat.
For example, it’s not unusual for premises to use flash coolers; compact chilling units that chill beer directly at the point of service. They’re popular in establishments where draught beer needs to be served cold but refrigeration options are limited as flash coolers push chilled air into the cellar to produce an optimum temperature for the storage of beer, wine, etc. However, the heat generated from the cooler is expelled into the cellar, and usually, there will be a soft drinks plant expelling air into the cellar as well. Taking a 5kW beer cooler and an 800w from a soft drinks plant, you have the equivalent to the heat generated from a typical boiler from a 2-3 bedroom house. This is comparable to leaving all the doors and windows open with the heating cranked up. Farcical; wasteful, energy-intensive, and expensive!
One method of getting a cellar to beer temperature is to use a heat dump fan unit which displaces the heat to the external atmosphere, outside of the beer cellar. This is by far an improvement on heating the cellar with the very unit required to cool it down! Also becoming more popular is a single compressor supplying the cooling to each beer remote (the cooling bath the beer passes through).
But when a cellar has 3 remotes, which is entirely possible, three separate remotes with all the associated equipment and pipes are required. This becomes energy intensive.
-
Each 4.4kW of cooling system requires 4.83kW p/h x 3 (remotes) = 14.49kW p/h
-
Given an average run time of 9 hours per day = 130.kw per day for x 3 units
-
Assuming a cost of £0.25 per kW/h = £32.50 per day – just for cooling the drinks
In larger venues where power consumption is always a significant consideration, it often makes financial sense for the building owners to buy their own pack system rather than relying on the free systems provided by the beer industry. Owner systems tend to be more energy efficient and pay themselves off relatively quickly, whereas industry-supplied systems tend to be less energy-efficient but represent a cheaper option for the supplier. This sector has seen a step change where one piece of cooling equipment can power multiple beer remotes and that means less pipe work, less equipment, and more energy efficiency, and building owners are becoming increasingly savvy to this option.
There is an energy saving to be had by running on a pack system over individual cooling units or heat dumps, although the level of savings will depend on usage and atmospheric conditions.
-
14kW cooling system = 10.97kW p/h
-
Given an average run time of 9 hours per day = 98.73kW per day
-
Assuming energy costs at £0.25 per kW/h = £24.68 per day
Whilst a pack system offers an improvement on energy usage, it still generates 98.73kW of heat which is displaced to outside the building where it simply blows away. Meanwhile, establishments are using additional power to heat the venue and provide hot water.
